Functionality, cycle time, production rate and scrap volume improved for a metal stamping plant in Litchfield, Mich. after retrofitting an existing robot system with Magswitch® magnetic grippers. The robot system, which previously operated using two three-jaw grippers, experienced significant improvements in productivity and waste generation after the installation of four Magswitch M4040 HDC units.
Originally commissioned as a machining center with the ability to handle only one size engine dampener, the plant needed to run nine different sized units. To address this, the company first considered manual loading of the eight additional style parts. Although the plant’s engineer considered grippers to automate the process, he quickly realized they would need 16 new grippers that required a tool change for each style part. At a cost of approximately $5,000 per gripper in addition to fixture costs, the retrofit estimate was fast approaching $100,000, far exceeding the budget.
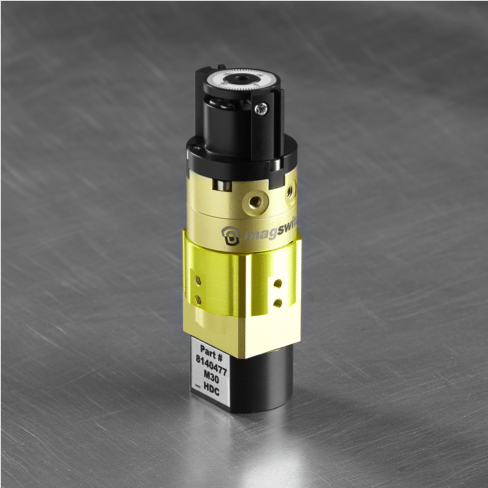
Magswitch M Series
In light of this reality, the engineer turned his sights on Magswitch industrial magnets. By using only four M4040 HDC tools, he could build one fixture to handle all of the different parts. The magnets, which provide more forgiveness for locating, not only aided in reducing the robot part pick time, but allowed for more flexibility in the cell—the ability to run all of the parts without a lengthy changeover. The tool change also reduced scrap and potential injuries by eliminating the need for operators to handle the 45-pound parts.
View the application video here or click on the image above.